From 2025, the Future Homes Standard will require new-build homes to have low-carbon heating and conform to demanding levels of energy efficiency. The aim is a 75 to 80 per cent reduction in carbon emissions compared with homes built under the current Building Regulations.
In addition, local planning authorities are also likely to make increasing demands to improve the environmental performance of new buildings of all kinds. If that wasn’t enough, many clients will be concerned about embodied carbon and how to reduce the amount involved by reuse of materials that have in the past been discarded.
To meet these goals, developers and their supply chains can take a number of approaches, including improving heating systems and replacing familiar technologies with low-carbon alternatives.
These pressures will demand innovation as the industry grapples with radical changes to ways in which it has long worked.
Among the problems, though, is that innovation is costly in itself. A lot of time can be tied up in research and development (R&D), with the outcome always uncertain – a process of finding out what works and what doesn’t before any new material or technique can be put to use and earn money for a developer and contractor.
The government has recognised this difficulty and is supporting R&D work through tax credits.
However, like anything else that involves access to public support, companies must convince HM Revenue & Customs (HMRC) that the money involved was genuinely spent on R&D and not just a tweak to accepted best practice.
Iain Butler, a director of Buzzacott, has long experience in guiding construction firms through the R&D tax-credit maze and expects the Future Homes Standard and other changes demanded by planners to produce many new contenders for the credits.
He explains that a small company could recover 20 to 25 per cent of its qualifying R&D costs – either in a tax saving or cash – while for larger firms with 500 or more employees the rate is 11 per cent. But what constitutes a ‘qualifying cost’ is a matter for some negotiation.
Butler says: “Construction-industry businesses are having to come up with innovative ways of working, either within an already designed building, or with embodied carbon when taking an existing building apart, and trying to then retain as much of it as possible. That’s pushing up costs and the R&D credits can help them budget by indicating which innovation costs they can offset from tax.”
Qualifying for an R&D tax credit does not require an entirely new invention, as novel adaptations of existing techniques can be accepted. “It’s projects where you’ve got real head-scratching that count,” Butler says. “Where you’re maybe combining systems and technologies in a novel way, or developing parts within those that are new or different.”
Examples might include managing smoke within a building differently to meet a new fire regulation, or attempts to reduce solar loading.
Dealing with embodied carbon will require new ways to reuse materials and a new process to deconstruct a building, rather than simply demolishing it.
Butler sees some reluctance to innovate, as construction firms often fall back on traditional best practice. But he says: “For new demands coming through, the best practices are just not applicable.”
Sound advice on R&D credits is vital as HMRC is making more frequent and random inquiries about R&D tax claims and may want to interview the senior technical people within a company about what has been done.
Butler concludes: “R&D is something companies need to be thinking about, even if it’s not right on their agenda at this moment.”
SPONSORED BY BUZZACOTT
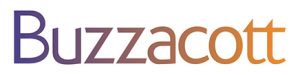
- For more information about collaborating with Construction News, contact maria.gonzales@emap.com